ALAŞIM
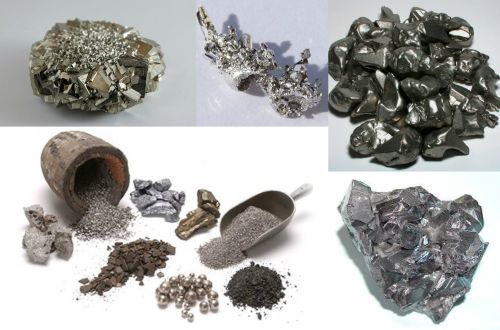
a. Bir metale bir ya da birçok bıı alaşımın katılaşması element (metal ya da ametal) katılarak el sırasında elde edilen yapılar de edilen metalürji ürünü; bu işlem metalin bazı özelliklerini değiştirmeyi, hatta ona yeni özellikler kazandırmayı amaçlar.
Sponsorlu Bağlantılar
—Polim. Polimerler karışımı.
—ANSİKL. Metalurj. Alaşımın fiziksel, mekanik ve kimyasal (aşınmaya dayanım) özelliklerini iyileştirmek için, taşıdığı elementlerin sayısı, yapısı ve oranı değiştirilir ya da kendisi çeşitli ısıl işlemlerden geçirilir. Ne var ki, bileşenlerin, yapıları ile miktarları arasındaki bağıntılar ve alaşımların özelliklerine etkileri karmaşıktır. Örneğin iki ya da birçok elementin ayrı ayrı etkisi birbirine eklenemez.
Mendeleyev sınıflandırma çizelgesinde yer alan hemen bütün elementler alaşımların bileşimine girer. Dolayısıyla kuramsal olarak şu sonuca ulaşılır: iki bileşenli yaklaşık 5 000 (ikili alaşımlar) ve üç bileşenli 100 000’in üstünde alaşım (üçlü alaşımlar) vardır.
Bununla birlikte bir alaşımda, % pil ya da % 0,01 'den yüksek oranda yer alan temel bileşenler ile birkaç p.p.m.’lik (milyonda bir) yan bileşenleri birbirinden ayırmak gerekir. Ayrıca yan bileşenlerin görevi ihmal edilemeyecek kadar önemlidir: örneğin yaklaşık 200 p.p.m.oranında itriyum katkısı, demir, nikel, krom ve alüminyumdan oluşan ateşe dayanıklı kimi alaşımlarda koruyucu oksit katmanlarının yapışma özelliğini önemli ölçüde artırır.
Alaşımların hazırlanması.
Alaşımların çoğunu eritme yöntemiyle hazırlama olanağı vardır. Bur unla birlikte alaşımın bileşenlerini hazma teknikleri,yapılarına, oranlarına, fiziksel (erime sıcaklığı) ya da kimyasal özelliklerine (yükseltgenebilirlik) göre farklılaşabilir. Aynı sıcaklıkta eritilmiş iki ya da daha çok metr.t ya da ametalin karıştırılması çoğunlukla yüzlerce derecelik sıcaklık artışına yol açar. Dolayısıyla olay sanıldığı gibi olağan bir karışım tepkimesi değ;t aksine ien<mi güç kimyasal tepkimeler zinciridir Kaldı ki erime sırasında biieşenienn eritme potalarının astarı, fırın tabanı ya da çevıe ortamla tepkimeye girmesi yüzünden alaşımın anma bileşimi değişebilir; üstelik ur cu elementlerin (çinko, magnezyumu bileşim içindeki oranı her an farklılaşabilir. Bu nedenle alaşım hazırlanırken uygu'anan metalurjik işlemler sırasında bileşenlerin çevrel ortama karşı korunması zorunludur. Bu amaçla çeşitli teknikler kullanılır: en önemlisi boşlukta (vakumda) gaz ya da sıvı akışı altında eritme ve dökümdür.
Öte yandan alaşımın anma Dİleşimi sık sık denetlenir. Oranlar çoğunlukla eritme fırınında element katılaıak ayarlanır ve hızlı tayfçekim çözümlemelerine başvurulur.
Alaşım, metalden yapıımış külçe kalıplarına dökülür, kalıplar ateşe dayanıklı bir bileşikle (silis, alüıı.in) kaplı ya da çıplak olabilir. Elde edilen külçelerin ağırlığı 5 kg’ia (laboratuvar deneyleri için) 70 t (demir-çelik fabrikaları için) arasında değişir.
Az çok homojen bileşimde bir sıvı alaşımın katılaşması, önemli yapısal ayrılıklar doğurur. Öncelikle sıvı halden katı hale dönüşümden kaynaklanan hacim büzülmesi, boşluk oluşumuna yol açar; bu kusuru gidermek için ya külçeyi yeniden ısıtma yoluna gidilir ya da "sürekli döküm"e başvurulur. Ayrıca, külçenin bir kesiminden öbürüne katılaşma sıcaklığı değiştiğinden çok farklı kristalleşme bölgeleri ortaya çıkar Kalıp çeperlerine yakın bölgede (külçe kabuğu) kristaller küçük ve küre biçimindedir; oysa külçenin ana kütlesi, merkez bölgesi dışında uzun ve ince kristallerden oluşur; merkez bölgesindeyse kristaller yeniden küre biçimi alır, ama boyları daha büyüktür. Ayrıca katışkılar ile gazlar bu bölgede toplanır. Ortaya çıkan ham ürünlerden yarımamul ya da mamul ürünler elde etmek için dövme ve haddeleme işlemleri uygulamak gerekir.
Bazı alaşımlar, kalıbı doldurma özellikleri nedeniyle doğrudan doğruyaişlenebilir: dökümcülükte kullanılan alaşımlar bu türe girer. Döküm işlemi ya kum kalıpla (kumla kalıplama) ya da dökmek istenen parça biçiminde hazırlanmış metal kalıpla (kokil kalıpla döküm) gerçekleştirilir. Ayrıca karmaşık parçaları yapmak için basınçla kalıplama yöntemine başvurulur; bu yöntemde sıvı ya da kıvamlı metal, kalıba basınçla püskürtülür: örneğin demir, nikel Ve krom alaşımlarından yapılan dış protez armatürleri bu teknikle elde edilir; bilindiği gibi değerli ya da yarıdeğerli metallerin çok pahalı olması yüzünden dişçilikte bu alaşımları kullanma eğilimi vardır.
Öte yandan bütünüyle farklı bir ilkeye dayanan başka bir yöntem geliştirildi: bu yöntemde preslenerek tıkızlaştırılmış metal tozları, katı ya da kısmen sıvı fazda sinteriendi. Böylece 1922’den sonra tungsten karbürlü "sinterlenmiş sert îlaŞımjar" elde edildi. Bu alaşımlarda Ipngsten karbürle ateşe dayanıklı başka karbürler birleştirildi (titan, molibden, tantal karbürleri) ve bağlayıcı oiarak çoğunlukla °/o.5 ile 10 oranında kobalt kullanıldı. Sözkonusu alaşımların Vickers sertliği 1 600 dolayındadır (yumuşak çeliğin Vickers sertliği 100'dür). Bu nedenle kesme çakılarının yapımında bu alaşımlar kullanılır ve çakıların yararlı ucuna (ağız) ince levhalar biçiminde takılır; kullanım soteleriyse aynı koşullarda hız çeliklerine oranla on kat uzundur. Öte yandan aynı alaşımlar maden ocağı takımlarının, tel çekme haddelerinin, metal tozlarını presleme kalıplarının, kumlama makinelerinde memelerin yapımında büyük ölçüde kullanılır.
Elmaslı alaşımlarsa, elmas tozuyla metal tozu,karıştırılarak toz metalürjisi yöntemleriyle hazırlanır; metai tozları bu alaşımın ya da sözde alaşımın iskeletini oluşturur. Bu tür alaşımlar alet (taşlama taşı, matkap) yapımında kullanılır; bu nedenle temel bileşimlerinde demir-nikel-krom, tungsten-bakır-nikel, özellikle tungsten karbür, titan karbür ve kobalt yer alır. Sözkonusu ürünlerden yapılmış aletlerle çok sert ve yıpratıcı gereçler işlenir (cam, porselen, değerli taşlar, su verme ve nitrürlemeyle sertleştirilmiş yüzeyler).
Alaşımların özellikleri.
Alaşımların özellikleri, sanıldığı gibi, bileşenlerin özelliklerinin ortalaması değildir. Örneğin bir alaşımın erime noktası, onu oluşturan arı metallerin erime noktalarından düşüktür. Buna karşılık temel birleşenlere oranla daha sert, dövülgenlikleri ve sineklikleriyse daha zayıftır. Ayrıca alaşımlar genellikle bileşenlerinden daha kötü iletkendir. Nitekim direnç üretiminde özgül dirençleri ‘arı metallerden daha yüksek,ama sıcaklık değişimlerine daha az duyarlı alaşımlar kullanılır. Ne var ki bu özellikleri genelleştirmede acele etmemek gerekir; çünkü gerçekleştirilen yeni alaşımlar (Invar, Constantan) sözü geçen gözlemlerin her zaman geçerli olmadığını kanıtlamıştır. Alaşımların temel yararı arı metallerden farklı fiziksel (özgül kütle, ısıl ve elektrik iletkenlik, manyetik özellikler, renk), mekanik (çekmeye, sertliğe, akmaya ve rezilyansa dayanım) ya da kimyasal (aşınmaya direnç) özellikler göstermesidir. Kullanım özellikleriyse çok sayıda etkene bağlıdır.
Önemli olan her şeyden önce alaşımın anma bileşimidir; bir fazlar diyagramıyla bu bileşikte yer alan bileşenlerin yapısı, kimyasal bileşimleri ve oranlan her fazda tanımlanır; tanımlamada ayrıca alaşımın hazırlanışı sırasında termodinamik dengeye uyma koşulu aranır. Öte yandan katı çözeltiler, ara fazlar ya da tanımlı bileşikler farklı katı fazları oluşturur.
Nihayet alaşımın mikrografik yapısı gündeme gelir; bu yapı-ısıl, mekanik ya da ısıl-mekanik işlemlerle her an değiştirilebilir. Genellikle fiziksel, kimyasal ve mekanik dönüşümler hızla gelişirken, yapısal dönüşümler çok daha yavaş gerçekleşir ve katı halde yayınım mekanizmalarına bağlıdır.
Alaşım elementlerinin çeliğin özellikleri üstündeki etkisi

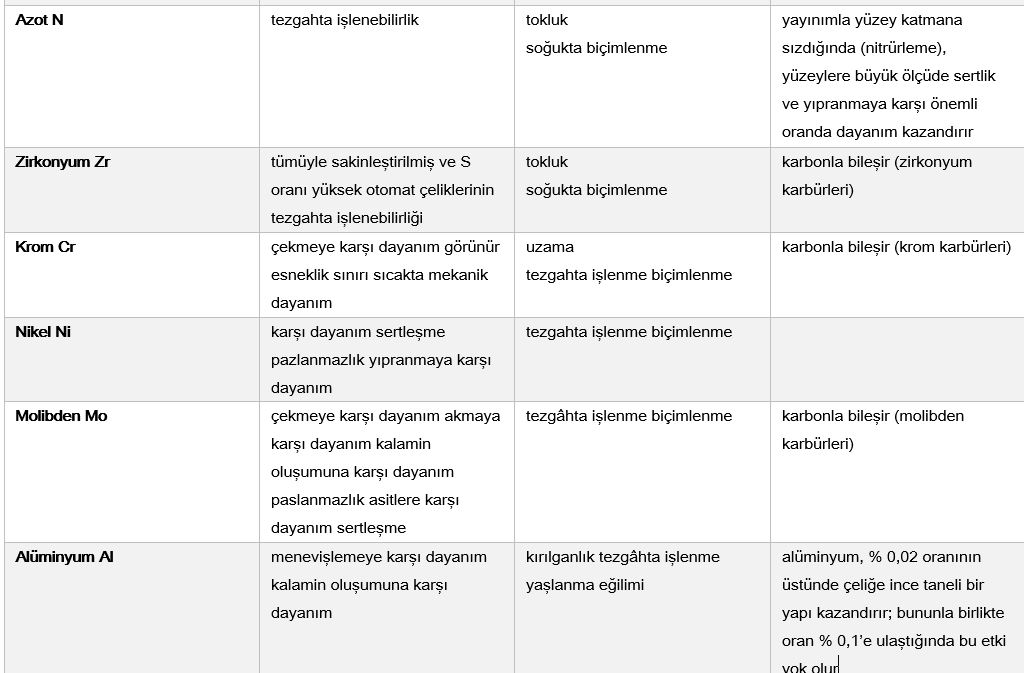
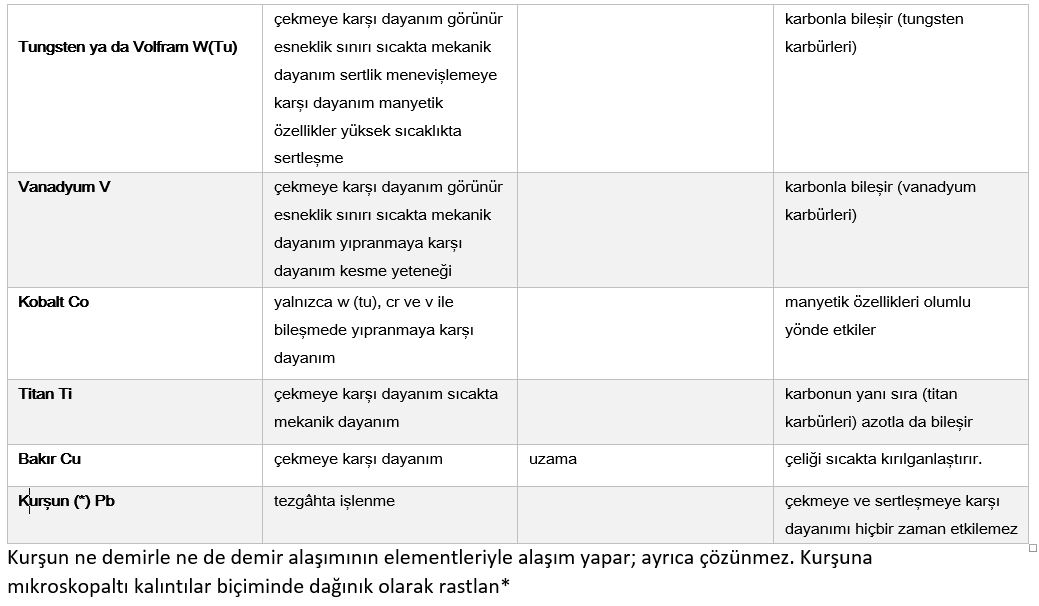
Alaşımların, katı çözelti ya da bir iskelet içinde çökelti fazları biçiminde oluşması, sertleştirme mekanizmalarının farklılaşmasına yol açar. Bu nedenle üretici, alaşımın temel metalurjik halini (ya da temel hal) açıkça belirtir; ham alaşım olduğu ya da soğuk sertleştirmeden geçirildiği, sıcak sertleştirmeden sonra tavlama ve kararlaştırma işlemleri uygulandığı, katı çözeltiyi izleyen tavlama ve menevişleme işlemleri vb gördüğü açıklanır.
Sanayi alaşımları.
Temel metale bağlı alaşımları içerir:
- bir ya da birçok ana katkı maddesinin oranı hem elde edilmek istenen dayanım özelliklerinin olası aralığını, hem de kullanım güçlüklerinin düzeyim belirler;
- çok sayıda ikincil katkı çok düşük oranlarda yer alır ve özgün işlevleri, kullanım özelliklerinin (mekanik, fiziksel ya da kimyasal) yanı sıra biçimlenme (soğuk ve sıcak biçim değiştirme, işlenme) özelliklerini de iyileştirmektir;
- ürünlerin hazırlanışı sırasında külçe kalıbına bağlı katışkılar.
— silisyum alaşımından ve demır-nikel-krom alaşımından söz edilir.Görüldüğü gibi sanayi alaşımları ya alaşımları oluşturan temel elementlerin adlarıyla (demır-krom, demir-krom-manganez alaşımları), ya kullanımda edindikleri özel adlarla (pirinç, bronz, Düralümin) ya da simgelerle belirtilir (ürünlerin yapısını, bileşimini, ısıl işlemleri belirten norm ve standartlar). Öte yandan sayılarının çokluğu nedeniyle alaşımları, temel metali (alüminyum, nikel, kurşun vb.) göz önüne alarak sınıflandırmak da yerinde olur.
—Parac, Eski çağlarda para alaşımlarının temeli altın ve gümüştü. Anadolu'daki bazı paralar, altın ve gümüşün doğal, ya da yapay bir alaşımı olan elektrum'öan yapılmıştı. Para basımında kullanılan alaşımlarda XIX, yy.’ın sonuna dek pek bir değişiklik olmadı. Ana maddeler hep altın, gümüş ve tunç idi. Metalurj eki gelişmeler, XX.yy.'ın başında, nikeı,n saf ya da bileşik olarak (bakır-nikel alaşımı, mayşor, daha sonra alüminyum tuncu) para basımında kullanılmasına vol açtı, iki dünva savaşındaki maden kıtlığı, para yapımında yeni alaşımların kullanılmasını gerektirdi. Alumag (magnezyumla sertleştirilmiş alüminyum), Zamak (alüminyumla sertleştirilmiş çinko), hatta yumuşak demir farmako demiri). 1950'den bu yana teknilişmeler, paralardaki alaşımlara paslanmaz çelik ve kaplanmış metalleri de k attı.
—Polim. Metallere özgü bu terimin anlamının zorlanarak genişletilmesine karşın, "alaşım” sözcüğü belli özellikler taşıyan polimer karışımlarını belirtmek için gittikçe sık kullanılmaya başlanmıştır; bu karışımlar kimi zaman İngilizce "polymer biends" ya da "multipolymer systems” adları altında tanımlanır. Genellikle, iki polimerin karışımı arayüzeyler düzeyinde zayıf bir bağlanma gösteren iki fazdan oluşur; bu yüzden orta düzeyde özellikler sunar. Bununla birlikte, bazı polimer alaşımları, ilginç özellikler taşır; bu özellikler bileşenlerin türüne ve her birinin doldurduğu hacme bağlıdır. Polimerlerden biri sürekli bir örgü oluşturur; öbürü ise bu örgü içinde küre, elips ya da lif biçiminde dağılmış taneciklerden oluşan süreksiz bir faz gösterir. Alaşımın özellikleri belli bir sistemi karşılar ve büyük ölçüde karışımın yapısına bağlıdır; nitekim, eşit oranlarda karıştırılmış iki A (bükülmez) ve B (esnek) polimeri, A içinde B küresei tanecikler biçiminde dağılmışsa bükülmez bir alaşım, B içinde A dağılmışsa esnek bir alaşım verir. Arayüzeyler düzeyinde iki polimerin bağlanma gücü alaşımın özellikleri üstünde büyük etki gösterir. Alaşım hazırlamada, doğrudan karıştırma işleminden, bir polimer eşliğinde bir monomerin polimerleşmesine değin birçok yöntem vardır Alaşımlar bağdaşık polimerlerin (yani iyi bir karışma gösterenler) karışımıyla sınırlı değildir; nitekim hiç bağdaşmayan polietilen ve polistiren bir bağdaştırıcı katılarak alaşım haline getirilebilir. Günümüzde bilinen birçok alaşım arasında (1980'de otuza yakın) şok (darbe) polı- stirenleriyle (polistiren - polibütadien) vinil poliklorür alaşımları ve bütadien - akrilo- nitril eşpolimerleri sayılabilir.
Kaynak: Büyük Larousse
Son düzenleyen Safi; 18 Haziran 2018 00:16
Tanrı varsa eğer, ruhumu kutsasın... Ruhum varsa eğer!